Project Name: Cargill Kooragang Loading Area
Project Overview: Complete design and construction of the load-out awning and heavy-duty pavement, including the removal and replacement of existing pavement.
Project Location: Kooragang Island, NSW
Type of Shed/Solution: Industrial Awning and pavement
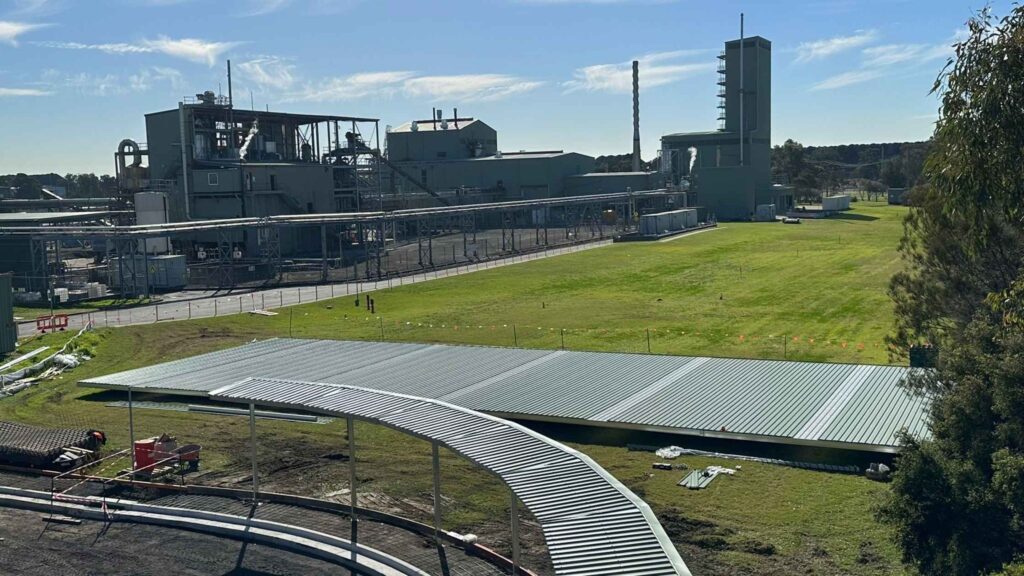
Project Overview
Cargill’s food manufacturing operations required a durable load-out awning and heavy-duty pavement replacement at their Kooragang Island site. Asset Building Systems delivered a full design and construction solution, including the removal and replacement of the existing pavement.
Our goal was to optimise Cargill’s loading area by constructing a weather-protected load-out awning and installing heavy-duty pavement. These improvements aimed to enhance vehicle access, product handling, and long-term infrastructure durability.
The existing worn pavement required complete removal and replacement, while the awning had to be designed for weather protection.
Project Scope and Objectives
We developed a project scope that met the client’s operational needs and delivered the following objectives:
Provide a functional and weather-protected load-out area.
Replace and install new heavy-duty pavement to support heavy transport vehicles.
Enhance site safety and optimise vehicle flow.
Initial Planning and Design Phase
Our design team assessed the site, ensuring a practical layout for vehicle access and material handling. Key considerations included:
Heavy-duty pavement design capable of handling continuous heavy vehicle traffic.
Load-out awning design for maximum coverage and long-term durability.
Drainage improvements to prevent water pooling and erosion.
The final design integrated seamlessly into Cargill’s existing operations while adhering to Australian safety and building regulations.
Pavement Removal and Replacement
The existing pavement had significant cracks, making it unsuitable for continuous heavy vehicle use. The replacement involved multiple steps:
Excavation and Removal:
The old pavement was carefully excavated, and debris was removed from the site.Ground Stabilisation:
The sub-base was compacted and stabilised using high-strength materials to ensure a durable foundation.Concrete Pouring:
High-strength concrete was poured and levelled, creating a smooth, load-bearing surface.Curing and Surface Protection:
Proper curing techniques were applied to enhance pavement strength and prevent cracking.Load Testing:
The new pavement was tested to confirm its ability to withstand heavy trucks and equipment.
Load-Out Awning Construction
The load-out awning provided essential weather protection for vehicles and workers. The construction process included:
Foundation Preparation:
The foundations were excavated, and concrete footings were poured to support the steel framework.Steel Frame Erection:
Pre-fabricated steel components were assembled on-site using cranes, ensuring proper alignment and stability.Roof and Wall Installation:
The awning was fitted with insulated roofing panels to provide protection from rain and heat.Safety Enhancements:
We installed safety barriers, lighting, and reflective signage to ensure safe operations during loading activities.
Drainage and Water Management Improvements
The site experienced drainage issues, leading to water pooling in the loading area. We addressed this by:
Installing a revised drainage system to divert excess water away from the pavement.
Creating graded surfaces that channel water efficiently, minimising the risk of flooding.
Using durable, low-maintenance materials to reduce long-term repair need
Project Challenges and Solutions
Several challenges arose during construction, but our team implemented effective solutions:
Minimising Disruption to Operations:
Cargill’s facility remained operational throughout construction.Solution: We executed the project in phases to maintain access for vehicles.
Weather Delays:
Rain affected some construction activities, particularly during excavation and concrete pouring.Solution: We adjusted schedules and covered working areas to minimise delays.
Ground Stability Issues:
The sub-base required additional stabilisation due to soft soil conditions.Solution: We compacted and stabilised the base using specialised materials to prevent future settlement.
Main Features of the Completed Infrastructure
Protecting products and workers from weather during loading and unloading activities.
Designed to withstand constant heavy-duty vehicle traffic without cracking or deformation.
Minimise pooling of water and thereby reduce maintenance.
Includes anti-slip surfaces, safety barriers, and good traffic markings.
Sustainability Initiatives
We adopted a sustainable practice by sourcing materials locally and minimising waste. The introduction of recycled material aggregates in the concrete mix was instrumental in lessening the environmental load of the project. The drainage works also conserve water and help prevent soil erosion at the site.
Collaboration with Cargill
Throughout the project, we maintained open communication with the client. Weekly meetings and progress updates ensured the project met deadlines and client expectations. Collaboration during the design phase allowed for input on awning dimensions, safety features, and drainage improvements.
Final Inspection and Handover
The project underwent a thorough inspection, including load testing of the pavement and safety checks on the awning. Cargill approved the final structure, praising its durability and operational benefits. We provided a maintenance guide to help the client maintain the infrastructure in optimal condition.
Project Benefits
The upgraded infrastructure delivered significant benefits:
Improved Efficiency: The layout and durable pavement improved vehicle flow and reduced loading times.
Weather Protection: The awning ensures product and worker protection during inclement weather.
Enhanced Safety: The site now features safer loading zones with improved markings and barriers.
Long-Term Durability: High-quality materials ensure the infrastructure will serve Cargill for years.
Reduced Maintenance Costs: Improved drainage and durable construction reduce the need for frequent repairs.
Future Collaboration
Given the project’s success, Cargill has indicated interest in future collaboration, including potential site expansions and additional infrastructure upgrades.
Final Thoughts
The Cargill Kooragang Loading Area Project highlights Asset Building Systems’ expertise in delivering tailored industrial solutions. We successfully designed, constructed, and delivered infrastructure improvements that support Cargill’s operational growth and efficiency.
Looking for a customised infrastructure solution for your facility? Contact Asset Building Systems today for a consultation.