Commercial sheds and warehouses are great for businesses looking for storage of stock or equipment. They can even have offices and packing rooms as part of the floor plan, making them an all round business solution. If you’re considering expanding your business space, this definitive guide to commercial sheds and warehouses will provide all the information you need – from what they are and what they’re used for to design and pricing.
Speaking of pricing, most people want to know the price upfront – and we’re assuming you’re no different. So below is a quick guide to give you an idea, but remember there are many factors that influence price. We’ll cover these later in the guide.
WAREHOUSE COST GUIDES* | Typical lower cost/m2 | Typical upper cost/m2 | Cost range for 1000m2 building |
Warehouse building only | $600/m2 | $900/m2 | $600,000 – $900,000 |
Warehouse, floor, basic electrical, no amenities | $900/m2 | $1200/m2 | $900,000 – $1,200,000 |
Turnkey warehouse complete design and construct | $1300/m2 | $1800/m2 | $1,300,000 – $1,800,000 |
*These prices are a guide only. They are base prices and do not take into account all influencing factors.
Shed v Warehouse
Now that you have an idea on price, let’s look at the difference between a commercial shed and a commercial warehouse? . Generally, a shed is smaller than a warehouse and is used for storage and shelter for equipment and machinery. It can also be used as a workshop for a business. Warehouses tend to be larger structures for intensive storage and logistics operations. They also have space for truck access.
Both commercial sheds and warehouses provided enclosed spaces that are tailor-made for business activities. Key differences come down to scale and intended functions.
Some common uses for these buildings include:
· Warehouse space
· Packing and processing
· Storage
· Workshops
· Manufacturing
· Retail showrooms
· Aircraft hangars
· Indoor sports facilities
· Meeting spaces
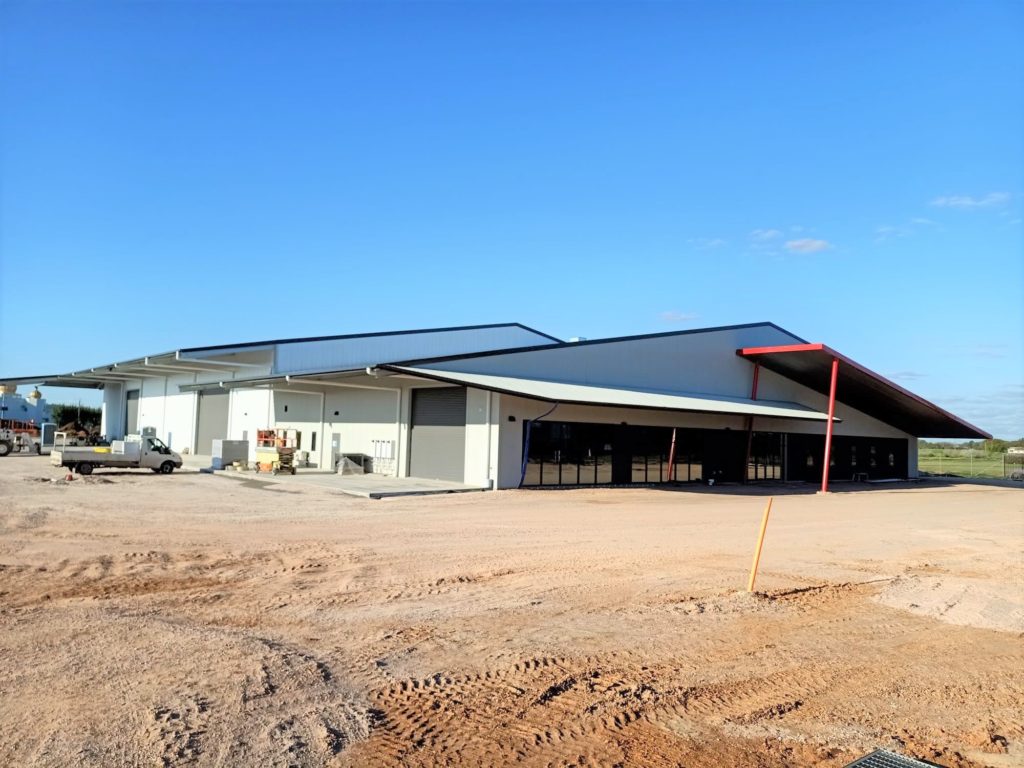
Advantages of a custom built commercial shed
Generic or standard-design commercial sheds might seem like convenient, cost effective options. But opting for a fully custom design brings advantages over the longer term. These include:
- Durability of materials used
- Flexibility of design
- Built to relevant regulations
- Optimised for current and future operations
- Optimal use of land
The process of building a commercial shed or warehouse
So, you’ve decided a commercial shed or warehouse is right for your business, and you understand the advantage of having one custom built, but where do you start? What’s the process for getting it built?
Site evaluation, design and planning – This is all about your goals and intentions for both the shed/warehouse and your business.
Gaining approvals – This is the stage where plans are finalised and submitted for approval by local government authorities.
Timeline Requirement – This is an important stage that sets the project up for success. It ensures the materials and labour are lined up for the right time, especially if needing the project completed in a tight timeframe.
Shed Foundations – As always, the foundations of the building and setting up of the site for optimal success is important.
Site Management and Safety – Safety, compliance and quality are critical factors that need to be attended to and monitored.
Frame and purlins – This is the stage where the building takes shape. Special fixtures and additions like fire proofing also occur now.
Shed roof and metal sheeting – This is the final stage in building the structure
Fit out and site clean up – The finishing touches including fittings are installed ready for the building to be used.
Inspections and compliance – Before you can occupy the building, inspections need to be carried out to ensure it’s compliant with all regulations.
Shed roof and metal sheeting – This is the final stage in building the structure
Fit out and site clean up – The finishing touches including fittings are installed ready for the building to be used.
Inspections and compliance – Before you can occupy the building, inspections need to be carried out to ensure it’s compliant with all regulations.